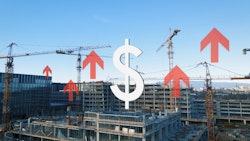
IRONPROS: What are the challenges of dealing with inflation in the construction industry?
Management Controls: Inflation adversely affects the price of construction/building materials and equipment; inputs like fuel, equipment and technology; and an evolving yet dwindling labor market—dwindling because so much of the workforce is aging out or leaving the sector.
These challenges lead to the price of bids increasing as profit margins of current projects decrease. Rising prices to offset wage hikes have also contributed to inflation. It’s a conundrum.
On one hand, U.S. industrial policies are favoring domestic manufacturing as we are amid a reshoring renaissance, which is a positive. However, finding enough employees and contractors to fill needed roles remains tough.
A survey by Industry Week of those in the field reported more than half of respondents planned to leave the manufacturing sector, citing discontent with available free time and wanting more flexible hours. Workers also want a more high-tech and sustainable workplace.
IRONPROS: What factors or aspects of construction projects should businesses look into when cutting or reducing costs?
Management Controls: The right technology enables businesses to automatically control, manage and reduce contractor labor, equipment and materials spending. For example, certain contractor-specific software automatically determines net billable hours and costs that manufacturers and contractors agree on before authorizing payment. Net billable hours and costs are accurate, transparent and reflect the work that is earned by contractors.
Businesses should also work toward improving safety. OSHA reports that working 12 hours per day comes with a 37% increased risk of injury. Further, fatigue-related, health-related lost productivity time at work costs employers an estimated annual $136.4 billion.
The right platform can help accurately monitor workers (and assets) to provide real-time fatigue violation alerts and data. For example, data can show if a contractor has been on the clock for 15 consecutive hours or for 15 consecutive days. Using real-time access gate data, onsite hours are tracked and flagged so lives and manufacturers are safer, enabling the latter to proactively mitigate risk by reducing dangerous overtime shifts or by sending a worker home before an accident happens.
IRONPROS: How can the Management Controls myTrack Platform help with cost control?
Management Controls: MCi’s myTrack, which is a contractor data and spend management platform, helps construction owners/companies streamline back-office processes and support greater overall productivity, job site safety, cost controls and strengthened contractor relationships.
With myTrack, companies can measure, track and make informed decisions about routine maintenance, shutdowns, turnarounds, outages and capital projects in one place. They can also gain real-time insights into their contractor relationships, ensuring compliance, accurate hour and dollar calculations and seamless integration with their ERP system. Contractors get paid accurately and on time, with labor and hours validated through access control and gated systems. Manufacturers can improve productivity, job site safety, spend visibility and build stronger owner-vendor relationships.
IRONPROS: What should construction professionals know about using this type of solution for their business or project?
Management Controls: myTrack’s real-time data insights enable companies to make informed decisions based on accurate information, leading to better decisions about future projects, budget allocations, contracting strategies and contractor performance evaluations.
It can help companies save millions of dollars on total contractor spend annually. One of our customers, a global mining leader that allocated 30%-40% of its costs to labor wages, for example, saved more than 12% on its annual contractor spend with myTrack. Its proprietary real-time insights, increased transparency and time-saving automation empower customers to save an average of 15% on annual contractor spend.
IRONPROS: What can customers expect from Management Controls in 2024?
Management Controls: As the industry continues to grow because of the government reinvesting in the U.S.’s manufacturing sector, so does the relevancy of contractor data and spend management software.
This onshoring momentum is being driven by three substantial pieces of federal legislation signed into law in 2021 and 2022:
1. The Infrastructure Investment and Jobs Act (IIJA)
2. The Inflation Reduction Act (IRA)
3. The Creating Helpful Incentives to Produce Semiconductors (CHIPS) and Science Act.
This combined legislation brought about domestic manufacturing change and growth with factory construction nearly doubling in one year. And while keeping track of contractors can be challenging without the right technology, solutions like myTrack enable manufacturers to track labor, equipment and materials expenses more efficiently. This game-changing technology also delivers real-time insights, increased transparency and time-saving automation to reduce significant costs.